Tool milling requires sharp precision and utmost accuracy. When you have clients asking you to fabricate custom tools and parts for specific uses, you have no room for error.
That’s what computer numerically controlled (CNC) milling machines are perfect for. These machines make these otherwise mentally taxing tasks 100% automated, and five times faster than when they are done manually. As long as the computer-aided design was programmed correctly, the margin of error in a CNC milling operation is virtually zero.
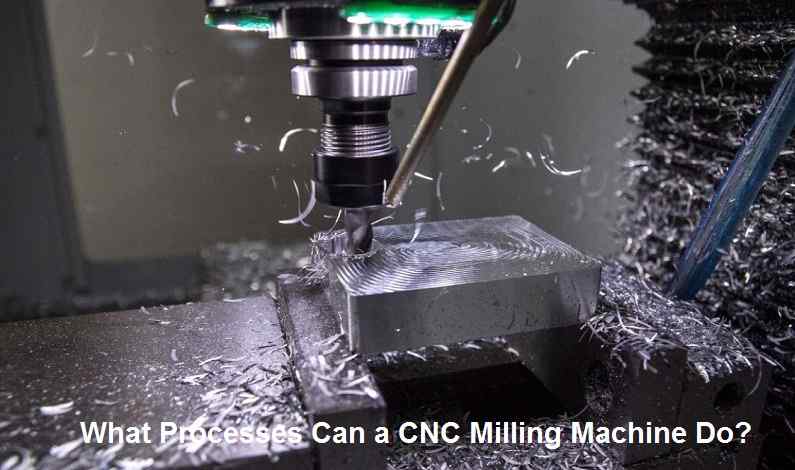
You’d also be amazed at the number of tasks that a CNC milling machine for sale online can do. There are various types of tool milling using CNC machines, and below is a brief discussion on each one.
Table of Contents
Different Types of Tool Milling Operations
According to Thomas.net, these are the different types of milling operations that a CNC machine can do:
-
Face milling
In face milling, the workpiece passes in front of the cutting tool itself during the milling process. The tool’s working path is perpendicular to the length of the blank used in the process. When your task is to create contours on the material, then you are most likely undergoing a face milling application.
-
Surface milling
Surface milling is the opposite of face milling. The cutting tool turns along the body of the workpiece as it passes by on a parallel line. It is a very complicated form of milling. Depending on the complexity of the intended product, an operator can expect to change cutters periodically as well as slow down or speed up the tool’s speeds accordingly.
-
Angular milling
If face milling results to contours, this process is used to create materials that have sharply angled features in its façade. A CNC milling machine can be used to introduce serrations and force grooves onto the surface of the workpiece as well as dovetails, among others. Operators add unusual angles when positioning the cutting tool against the workpiece.
-
Straddle milling
It is a complicated process that involves positioning a workpiece between two cutters. As its name suggests, the piece is “straddled” in-between two cutting tools. These tools cut through the blank in unison, resulting in a deep groove along both sides of the material.
-
Gear cutting
The name says it all. This milling process is explicitly intended to grind circular pieces of metal and produce gear teeth. This process creates cogwheels, automobile gear sets, and many others.
-
Gang milling
Gang milling is similar to straddle milling. It also employs two cutters working simultaneously on a single workpiece. However, this type of milling allows one of the cutters to grind or cut a different pattern from the other. This technique helps save time as opposed to having individual processes for each design on each side of the workpiece.
-
Form Milling
Form milling is as complicated as angular milling. This operation is fitting if the client wants the finished product to have irregular surfaces. Machine parts with both flat and curved surfaces are most likely fabricated using this process.
Take a minute to appreciate the diverse applications that any CNC milling machine for sale online can do. Investing in one of these tools opens your fabricating company up to a massive number of opportunities in terms of what finished products you can make for your clients.