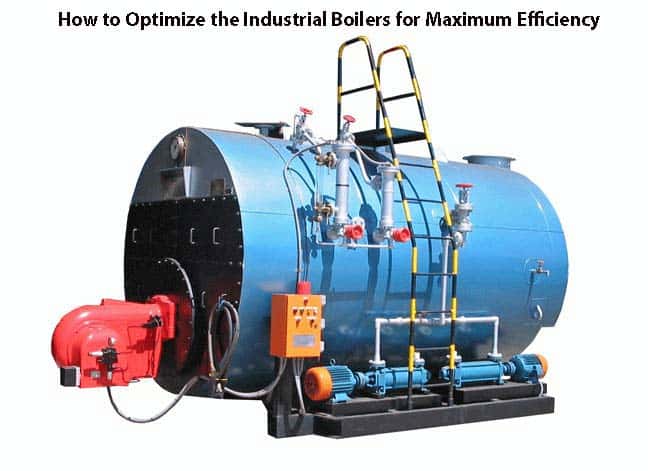
According to the U.S. Department of Energy and the American Boiler Manufacturers Association (ABMA), several boiler units and machines are operating five to ten percent of the below performance levels. Well, they can be more than three decades old and might not have industrial boiler controls integrated.
Typically, boiler fuel represents 30 to 50 percent of total energy budgets in plants. This also includes large thermal loads. Along with these, other maintenance costs and labor costs account for 15 percent of the expenses.
Thus, it is crucial to integrate boiler controls to increase the fuel optimization process.
The following are the essential pointers that help in maximizing efficiency by optimizing industrial boilers.
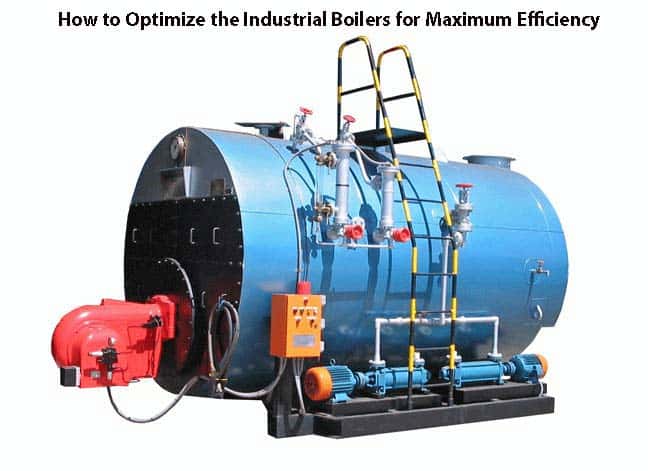
Table of Contents
A Perfect Fuel to Air Ratio
Optimization of combustion is possible by maintaining a correct ratio of fuel to air. Although ensuring an exact ratio is not realistic, if adequate control systems are put to use, then it can optimize the operations. Since combustion is a significant component of operations, you must allow a slight amount of excess air.
Too much air may lead to heat loss, and too little may prevent the combustibles from burning thoroughly. An oxygen sensor or transmitter in boiler control may help you to achieve the desired ratio to optimize the boiler.
Recovery of Heat for Redirection
A boiler unit may not function effectively if the heat generated is not efficiently disposed of. The heat must be put to redirection for reuse by blowdown. The boiler controls have an economizer that recovers the heat and boosts efficiency by 10%.
The operating conditions, boiler type, and fuel type are the major factors that determine the optimization process. A specific boiler unit requires a customized control system in redirecting the heat.
Eradication of Impurities and Foreign Particles
An industrial boiler, be it from the dairy processing unit or food processing unit, needs cleaning regularly. For this purpose, treating water is vital for the efficient functioning of the boiler.
Clogging occurs in internal tubes due to unwanted particles and dangerous substances. As a result, the ability to transfer heat reduces, and efficiency diminishes. Industrial boiler controls have a filtration system that prevents this problem.
The Decrease in the Warm-up Time
It is imperative to decrease fuel consumption and warm-up time. Achieving this is easy. You need to reduce the on and off cycles.
A boiler is optimized with an upgrade and a high turndown burner. Systematic functional planning can reduce the number of cycles and increase the operating purpose.
Annual Maintenance
As the boiler ages, the efficiency also decreases. New boiler functions as per the standards, but the older ones call for servicing. To avoid any malfunction in the boiler, you must maintain the unit regularly.
This ensures smoother function and effective productivity. Additionally, it does not incur hefty expenditure that you may incur if it breaks down. Follow the manufacturer’s guidance and keep the boiler in the best condition.
Lack of resources and funds should not be the cause of the boiler performance problem. Instead, work out the plan and install industrial boiler controls for promising functionality.